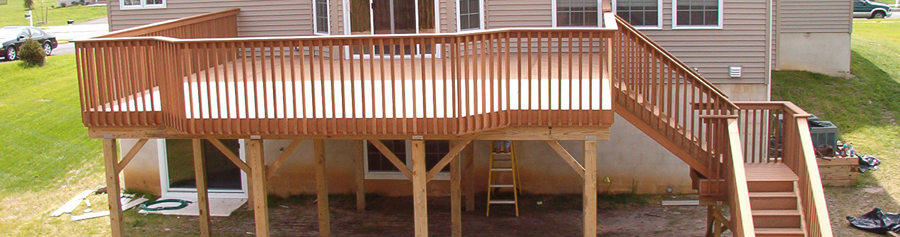
We have all read the headlines of tragic deck collapses over the years. The causes of these tragedies are typically either from inferior design, construction or from failures due to age and wear that went unnoticed.
According to North American Deck and Railing Association, from January 2000 to December 2006, there were 179 reported deck collapses. Of those, 1,122 people received injuries and 33 people died. According to the same source, reported deck collapses have increased at a rate of 21 percent per year over the same period. Most collapses occurred in the months between June and August when the decks are obviously in peak use and loading, while the other collapses that were reported over the winter months were typically due to excessive snow and ice loads. The failures occur when the structure can no longer resist the loading that is placed upon it.
Currently, the construction of a new deck is required by law to have proper permits and municipal inspectors to issue certificates of occupancy after the deck construction is complete. This requirement is based, at least in part, due to past deck failures resulting in injury or death. The current International Residential Code (IRC) is one of the primary references for both deck designers and code officials. Among other requirements, the code contains standards on how to properly design and construct safe structures. Unfortunately, however, there aren't any requirements for inspections of existing decks. The International Code Council does, however, recommend that exterior wood structures be inspected twice per year.
Improper Fastening Leads to Failures Experts agree that the main source of collapse is failure of the connection between the house rim joist and deck ledger as well as post or railing failures. It is estimated that 80 percent of the deck collapses occur at the ledger to rim joist connection, the location where the deck attaches to the building. Deck ledgers, (as seen in the accompanying photo), should be screwed or preferably bolted to the building rim joists not merely nailed. Bolts and screws can resist the expansion and contraction of the wood. They may, however, loosen over time. Early signs of such loosening are gaps between the house and deck. If nails were used, the deck may fail from this movement with no warning as nails cannot resist the above described movement.
Flashing installation is another important feature in deck construction. Flashing is the installation of metal coil to direct water out from behind building materials. Missing or improper flashing may allow for water to infiltrate behind the deck ledger and cause deterioration of building rim joist. This is a very difficult item to inspect through a non-invasive inspection. In addition, aluminum flashing should not contact pressure treated wood due to a highly corrosive chemical reaction of these two materials. New pressure treated wood uses alkaline copper quarternary (ACQ) chemicals for preservation, which is even more corrosive then previous treatments that were applied to wood. This means special attention must be given to all metal in contact with the wood. Aluminum will dissolve very fast in the presence of ACQ. This change in chemical treating also does not allow for making repairs to existing decks. ACQ in new wood will corrode existing connectors within three years. Decks need to be replaced in their entirety once decay has been observed.
Aging wood is not always the main problem. With proper construction and maintenance a typical deck should have a useful life of 20-25 years, depending on its construction and site (sun) orientation. Decks that lack sun exposure can degrade faster as the wood does not dry out especially if the wood is not being stained or painted. When wood degrades it loses its structural capabilities as well as the ability to hold a fastener.